こんにちは、アドラーです!
今回は新たに「QC検定の用語解説」として、「Excelで出来る品質機能展開(QFD)」という記事を書きました。
QC検定に合格するために、SQCを中心としたQC検定の体系的な勉強をしている方も多いと思います。その一方で、体系的なQC知識は書籍で学ぶことはできても中々その知識を実務に適用することが難しいと感じている方も多いのではないでしょうか。
今回の記事では「現役技術者が教える「QC検定の知識を実務に応用するための思考法」」で紹介した「ものづくりを変える」段階において必須の技術である「品質機能展開(QFD)」について紹介します。
私自身、QFDを実務に応用した事例をあまり社内でも社外でも見たことがありませんでしたが、外国サイトでちょうど良いテンプレートを見つけることができました。
本記事ではQFDとは何か?という概念的な部分を押さえてからExcelで実際にQFDを実践してみたいと思います。
資格勉強のみに留まらず、実務への応用に役立てていただけますと幸いです!
筆者のプロフィール・ブログ運営の理念は自己紹介からご覧ください!
目次
概要
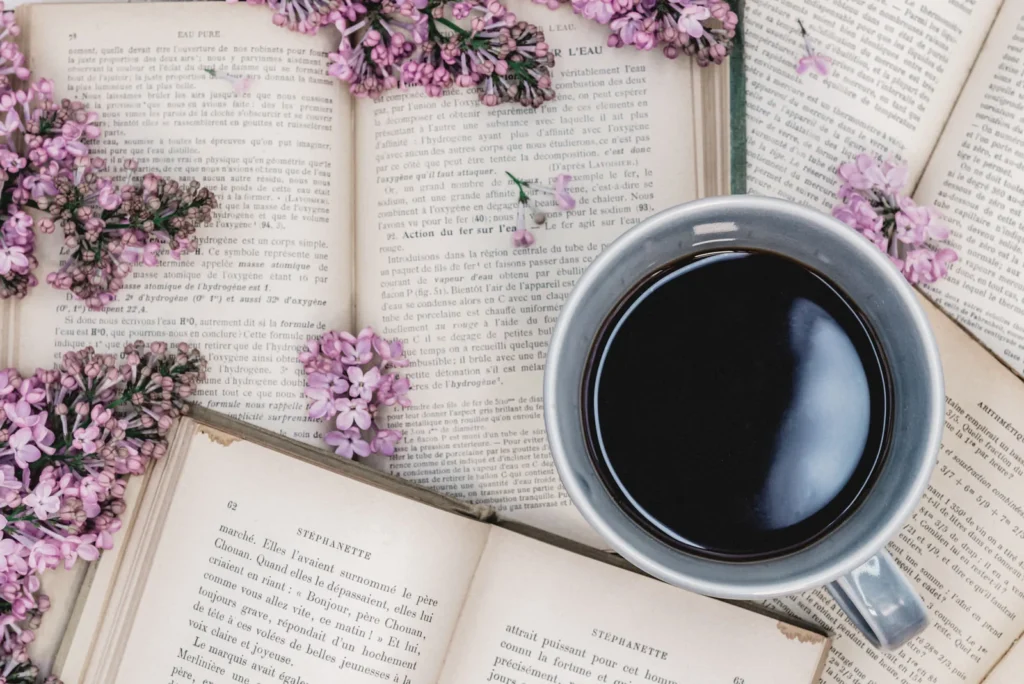
初めに本記事の概要を示します。
- QFDとは「顧客が望むもの(お客様の世界)を技術の世界に落とし込む手法」のこと。
- QFDは顧客の要望とミスマッチする技術開発を防ぐために行う。
- いきなり設計業務に取り掛かるのではなく要求品質を確認してから、具体的な品質設計に落とし込むという「順番」が重要!
トヨタ必須の17の品質管理手法を伝授 品質の教科書 [ 皆川 一二 ]から引用・一部編集
それでは一緒に勉強していきましょう!
品質機能展開(QFD)の定義と目的
QFDの定義
品質機能展開(QFD:Quality Function Deployment )とは、製品に必要な品質特性を決定するための技術であり、「顧客が望むもの(お客様の世界)を技術の世界に落とし込む」技術と言い換えることができます。
品質機能展開では、横軸に顧客が望むものを、縦軸に技術的な品質特性をとってマトリクス(テーブル)状に整理して重点的に開発が必要な項目を決めていきます。
QFDの目的
QFDの目的は「顧客の要望とミスマッチする技術開発を防ぐこと」です。
自動車開発を例に考えてみると、顧客毎に「デザインを好んでいるのか」「燃費を優先しているのか」「長期耐久性を気にしているのか」など様々なニーズが存在しており、どの項目を優先するのかは市場状況や社会からの要請によって大きく異なることでしょう。
多くの技術者は「すべての性能を良好なものにする!」と意気込んで開発を進めてしまいますが、そのような技術開発では限られたリソースにメリハリを持って投入できず、顧客の要望からかけ離れた製品を作ってしまうかもしれません。
したがって、製品開発ではいきなり設計に取り掛かるのではなく「どのような機能を持たせるか?」をはっきりさせるところからスタートする必要があります。
SQC(統計的品質管理)の重要性はよく取り上げられますが、SQCはQFDで定義された機能を効率よく開発する手段なので、SQCを使う前にQFDを行うことが重要です。
QFDのExcelテンプレートの紹介
CIToolkitの紹介
それでは実際にQFDを行ってみましょう。
今回はCIToolkitという団体が作成していたフリーのQFDテンプレートを用いました。
このテンプレートでは、特殊なツールも用いずにExcelでQFDを完結することが可能です。
このCIToolkitという団体の概要は以下のYoutube動画で紹介されているとおり、日常生活やビジネスの場で必要な分析支援ツールを紹介しています。
QFD用のExcelテンプレート
QFDのテンプレートは以下のリンクからダウンロードすることができます。
サイトURL:https://citoolkit.com/templates/quality-function-deployment-template/
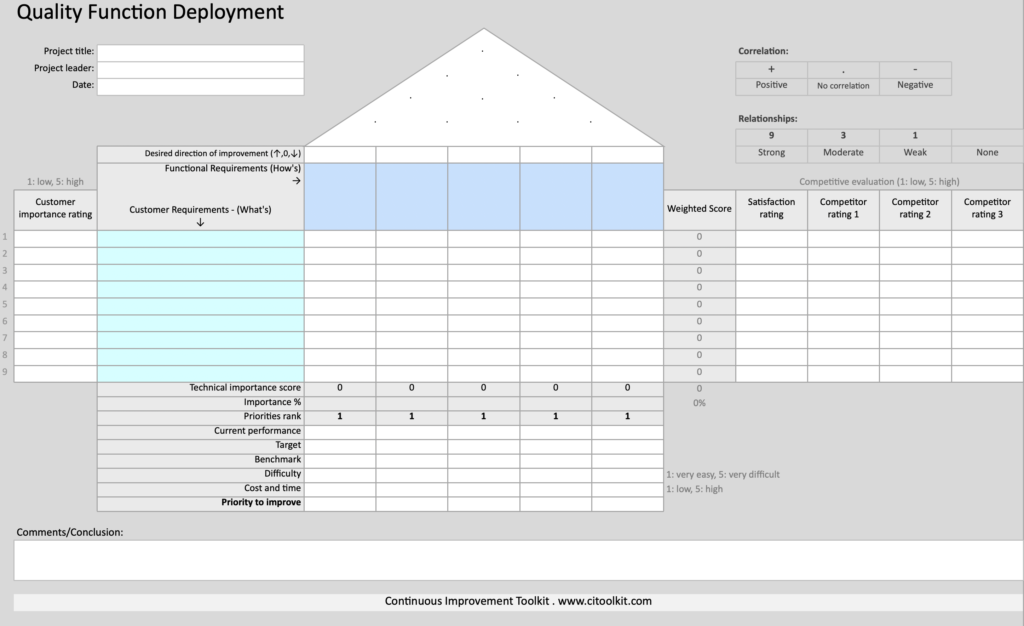
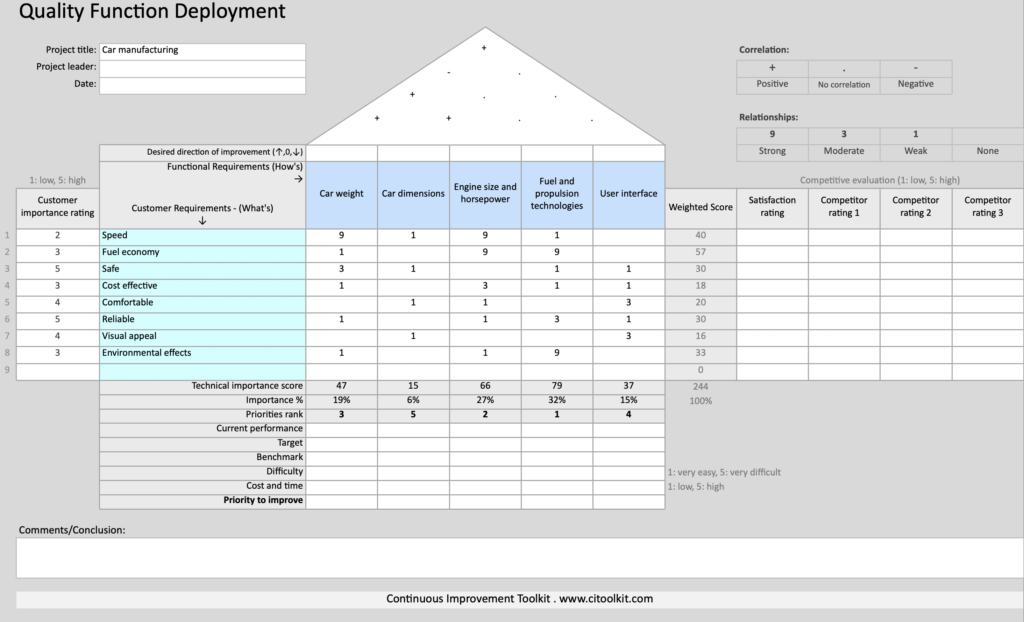
Excelを用いたQFDの手順と実践
それでは、ダウンロードしたテンプレートに沿って、「自動車開発」を事例にQFDの進め方を確認します。
品質機能展開は以下の①〜④の順番で行いますので、順番に確認していきましょう。
- 顧客の要求品質のリスト化と優先順位の決定
- 技術要素への展開
- 品質表の作成
- 設計目標値の決定
①顧客の要求品質のリスト化と優先順位の決定
ダウンロードしたQuality Function Deployment Template Example を見ていきましょう。
はじめに以下の図で赤色に囲んであるように「顧客の要求品質のリスト化と優先順位決定」を行います。優先度が高いものを5、低いものを1として優先順位をつけていきます。

実際に顧客の要求品質を定義するためには、アンケート調査などを行って顧客ニーズを引き出していきます。
今回の例では要求品質がかなり漠然としているので、実際のQFDでは1〜3次の要求品質まで細分化してみると良いでしょう。
例えば、「安全」という項目だけ取ってみても「バック時の安全機能」が必要なのか、「正面からの急な飛び出しに緊急停止できる機能」なのかといった場面別に細分化できますし、それぞれの技術に応じて達成難易度と要求度合いは異なりそうです。
1次要求品質 | 2次要求品質 |
---|---|
安全性 | バック時に後方確認しやすい機能 |
安全性 | 正面衝突を避ける機能 |
安全性 | 居眠り運転の危険を検知する機能 |
安全性 | 飲酒運転の危険を検知する機能 |
高次の品質機能展開は、各事業によって特性が異なるので、固有領域の知見が深い技術者や顧客との直接的な接点を持っている営業担当者との相談が必要です。
是非、簡易的な要求品質展開表ができたら部内で議論して、必要品質に漏れがないかチェックしてみましょう。
出来上がった要求品質表に「顧客にとっての重要度」を1~5で優先順位をつけたら要求品質展開は終了です。
今回の事例では「Safe(安全性)」と「Reliability(信頼性)」の重要性が高く、先進的な安全技術や故障に強いロバストネスが求められそうです。
技術要素への展開
次に要求品質を具体的な技術要素に展開してみましょう。
顧客の要求品質に対して、どのような設計品質(説明変数)を検討すれば解決できそうか、また要求品質項目との相関の大きさを記入していきます。
要求品質との相関の大きさは数字が10に近いほど相関が大きく、1に近いほど相関が小さいとします。
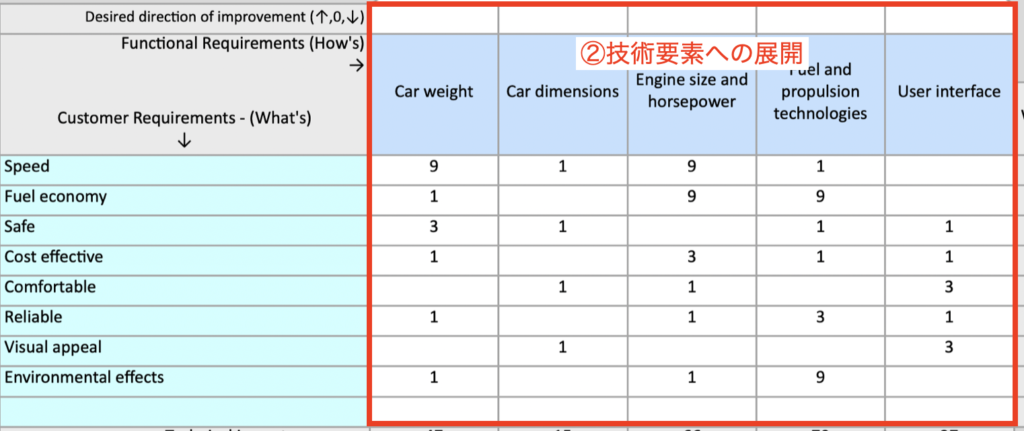
今回は以下の5つが設計で用いる技術要素になりました。
- Car weight
- Car dimensions
- Engine size and horse power
- Fuel and propulsion technologies(燃料推進技術)
- User interface
例えば、Car weightはスピードに大きく影響し、安全性にもそれなりの影響を持っているということがわかります。
軽くすればスピードは上がるので、望小特性(値が低いほど好ましい)特性と考えられますし、一般的に材料を軽量化すると安全性は損なわれでしょうから望大特性(値が大きいほど好ましい)と考えられます。
このトレードオフをどのように解消するかがこの開発の難しいポイントとも言えそうですね。
望小特性か望大特性なのか、相関関係が既に既知なのであれば9行目にも記入しておくと意思疎通や技術伝承が行いやすくなるので記入をしておきましょう。
③品質表の作成
次に品質表を具体的に作成しましょう。具体的には①で確認した要求品質と②で確認した技術要素から「対応の優先度(Priority)」を検討します。
このシートでは自動的に対応の優先度を計算してくれていますので、23行目のPriorities rankを確認しましょう。

以上の表では以下のように計算が行われています。
①Technical importance score:顧客にとっての重要度と技術要素の積和
②Importance:①の総和に占める各技術要素の重要度割合
③Priorities rank:②に基づく重要度
今回のQFDでは「Fuel and propulsion technologies(燃料推進技術)」の開発が重要になりました。
元々重要と考えていた「Reliability」と「Safe」の改善はできなさそうですが、燃料推進技術を改善することによって、顧客要求度がそこそこ高い燃費効率の向上や環境負荷の低減ができるので、製品開発の方向性は間違っていなさそうです。
④設計品質目標値の決定
③で完成した品質表・重点開発項目をもとに、目標設計値を決定していきます。
設計品質を考える上では、「競合との比較」、「自社の現在地点」、「技術開発の難易度」、「時間・マネーリソース」を勘案しながら競合を大きくリード可能な「ダントツ目標値」を議論して決めていきます。
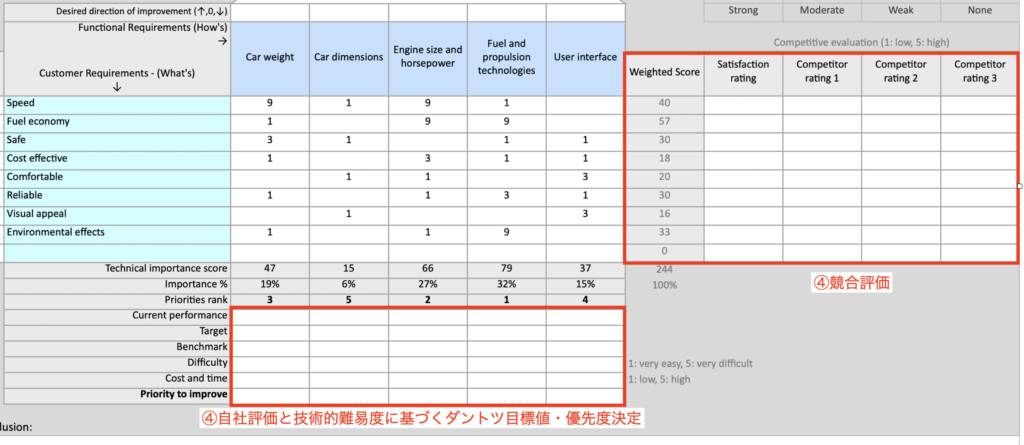
今回のケースでは「燃料推進技術」を重点開発テーマとしましたが、顧客の優先度が高い「Safe(安全性)」と「Reliability(信頼性)」に関しては技術要素として展開できていないことも将来的には競争力を落とす課題として認識しておく必要がありそうです。
他社に対して自社のSafe, Reliabilityが十分レベルにあれば開発を遅らせる、リソースを絞って次世代技術として少しずつ開発するということで問題はないですが、近々で技術開発する必要があれば、強みを持つ企業を買収することや期間限定で共同開発することで早期解決を目指すという方向性も考えられそうです。
QFDをすることで技術開発のテーマ絞り込みを効率的に進めたり、将来技術開発の方向性を検討できるので是非ご活用ください!
まとめ
記事のまとめは以下のとおりです。
- QFDとは「顧客が望むもの(お客様の世界)を技術の世界に落とし込む手法」のこと。
- QFDは顧客の要望とミスマッチする技術開発を防ぐために行う。
- いきなり設計業務に取り掛かるのではなく要求品質を確認してから、具体的な品質設計に落とし込むという「順番」が重要!
トヨタ必須の17の品質管理手法を伝授 品質の教科書 [ 皆川 一二 ]から引用・一部編集
更にケーススタディを行うことで、QFDは技術開発の方向性検討を行うことで、開発効率を大幅に上げられることを理解できました。
是非、本記事のテンプレートを使ってをQFDを行い、「技術開発の効率改善」に向けた議論を進めていただけると幸いです。
以下に本記事を作るのに参考とした書籍を紹介します。
統計学、QCの勉強におすすめの書籍ですので、「QCの知識をより高めたい!」という人はぜひ以下の書籍を読んで勉強していただけると筆者の励みになります。
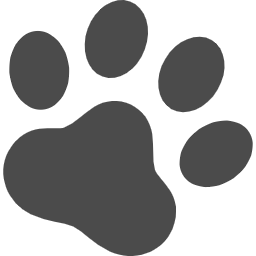
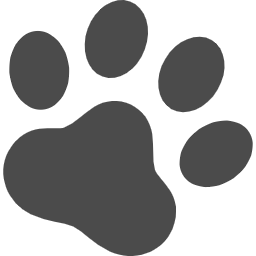
それでは最後に、私の大好きなドラえもんの言葉で今日の記事を締めさせていただきたいと思います。
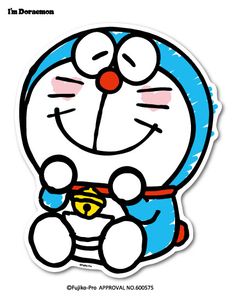
「なやんでるひまに、一つでもやりなよ」
— ドラえもん
今日もありがとうございました!