こんにちは、アドラーです!
今回は「QC検定1級論文対策シリーズ」として、品質不良を起こさない組織づくり〜品質を作り込む〜というテーマで記事をまとめました。
私のQC検定1級の合格体験談で紹介したようにQC検定では30分で750字の作文を書く必要があり、QCの本質を理解していることが重要です。
また、下記の通りQC検定1級を受験者の平均年齢は40歳程度なので、少なくとも係長以上の職責者が多いかと思います。

組織づくりの概念を学んでおくことは、管理職者の仕事を改善する上でも極めて重要になるので、試験合格のためだけでなく日々の仕事の改善に役立てていただけると幸いです。
筆者の詳細なプロフィールは自己紹介からご覧ください!
目次
前回の復習
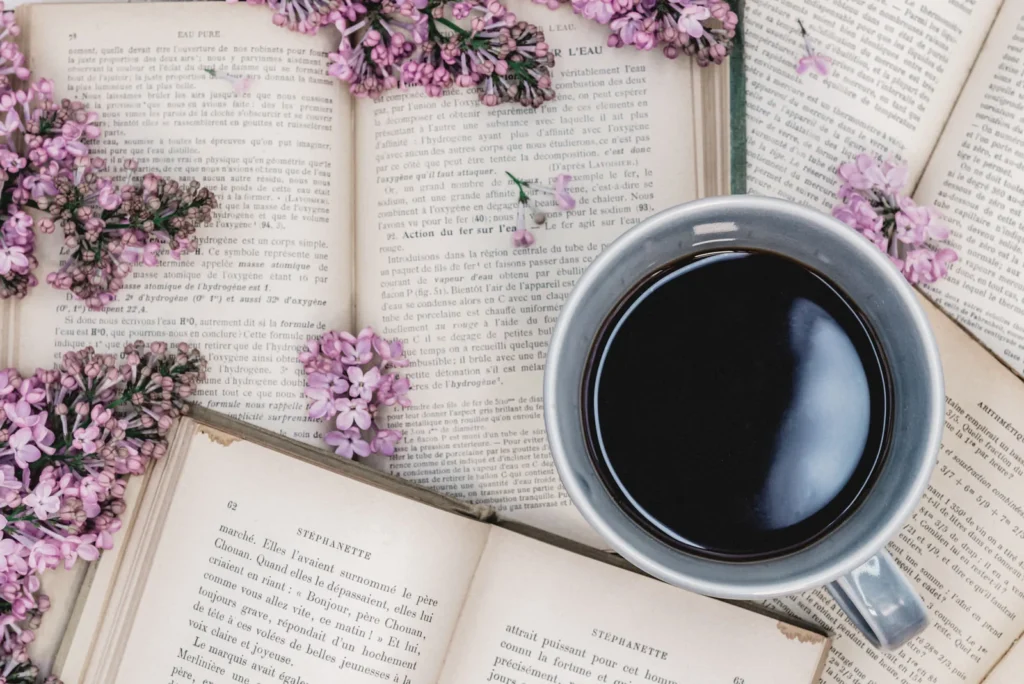
前回の記事では、品質管理(QC)のポイント、QC活動を行う上での重要な本質をまとめました。
- QCのポイントは「目標の明確化、達成度のチェック、対処」である。
- QC活動とは「顧客満足度(=品質)を具体的な数値で定義し、PDCAサイクルを回しながら改善していく活動」と言い換えられる。
- QC活動の上で重要な本質は「ファクトフルネス」、「ばらつきの統計的な管理」、「重点志向」
また、オススメの書籍としても「ファクトフルネス」「QC検定受検テキスト1級」なども紹介させていただきました。
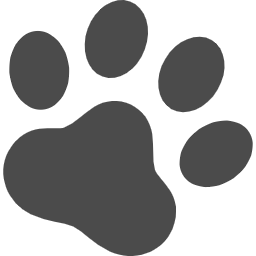
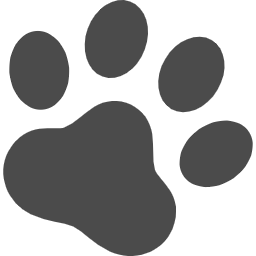
品質管理とは、「品質(≒顧客満足度)の目標値を明確にし、事実確認をしっかり行いながらPDCAサイクルを回し、製品・サービスを改善すること」と定義できますね!
本記事の概要
前回までのQC活動のポイントを押さえた上で、今回は品質不良を起こさない組織づくりをテーマにしました。
本記事の概要は以下の3点です。
トヨタ必須の17の品質管理手法を伝授 品質の教科書 [ 皆川 一二 ]から引用・一部編集
- 「品質を作り込む」とは「品質不良品を作らない」、「品質不良品を万が一製造しても市場に流さない」という2つの対策を絶えず行うこと。
- 上記2つの対策を行うためには、「人づくり」「仕組みづくり」「もの作り」の3つが柱となる。
- 品質不良を撲滅する上で最も効果的なのは「未然防止」であり、未然防止の実施には「フロントローディング」が有効
それでは、詳細な内容を見ていきましょう!
①「品質を作り込む」とは?
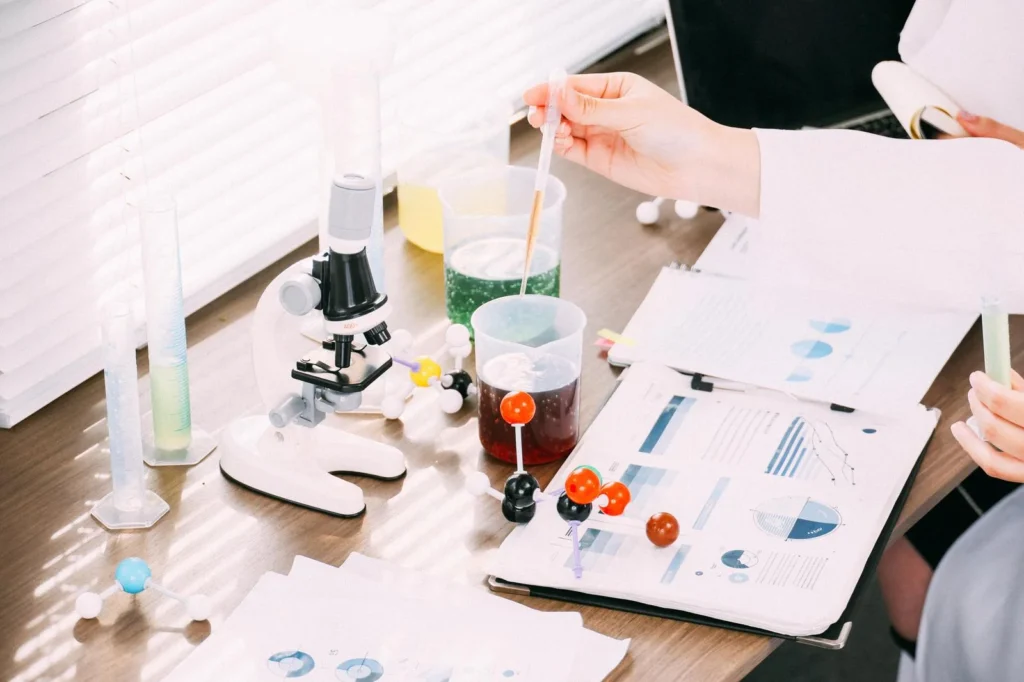
「品質を作り込む」とはどういうことでしょうか?
文字通り考えると、品質は「顧客の満足を得ること」として定義したので、「顧客満足度を得られる状態を作り込むこと」と言えそうですよね。
また、前回の記事で述べたように顧客満足は「購入時点」だけではなく「製品のライフサイクル全て」で満足を得る必要があります。
そのためには、筆者は2つの柱があると定義しています。
1つ目は「開発・製造工程で品質不良品を作らないようにすること」
2つ目は「検査工程で品質不良品を市場に出さないようにすること」
です。
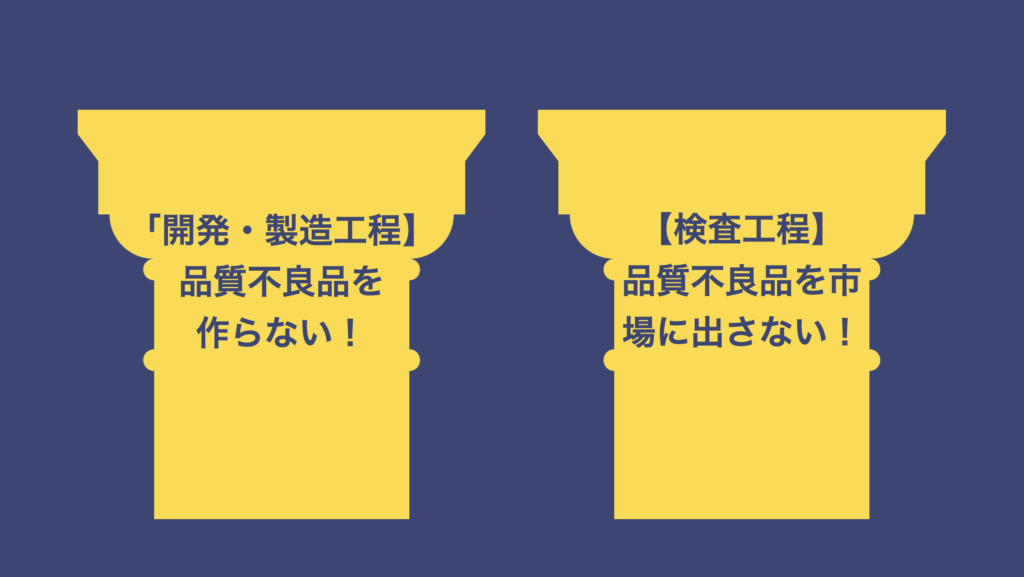
言い換えると、品質を作り込むとは「バリューチェーンの上流過程で2重に品質を管理すること」とも言えますね。
②品質を作り込むための3つの柱
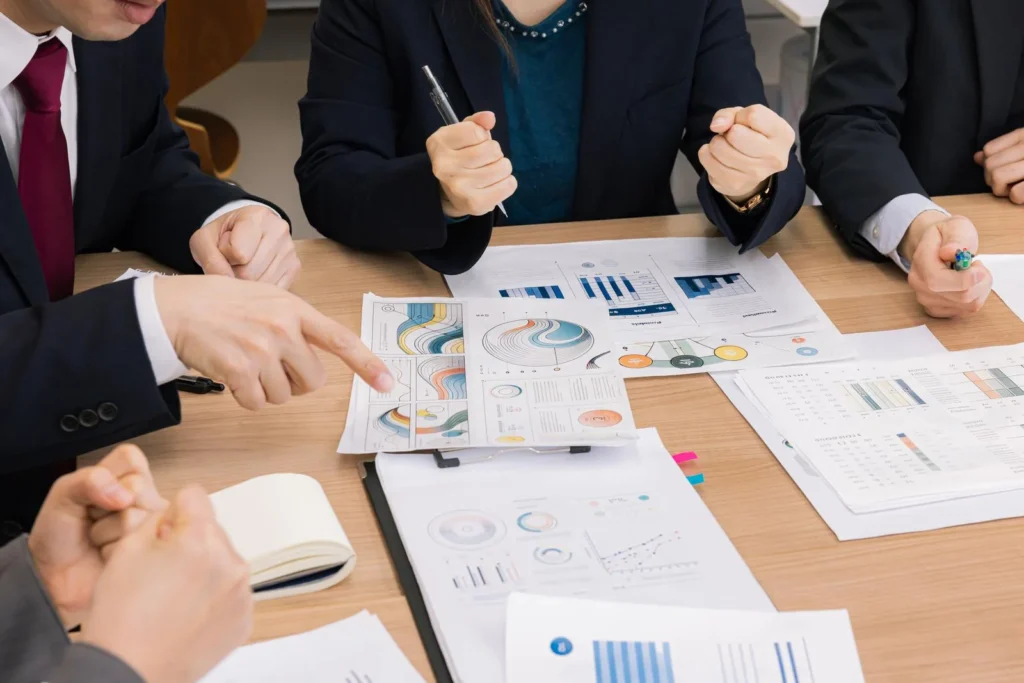
それでは、「品質不良品を作らない」、「品質不良品を市場に出さない」ことを徹底するためにはどうしたら良いでしょうか?
筆者は以下3つの力が柱になると述べています。
- 人づくり
- 仕組みづくり
- もの作り
トヨタ必須の17の品質管理手法を伝授 品質の教科書 [ 皆川 一二 ]から引用・一部編集
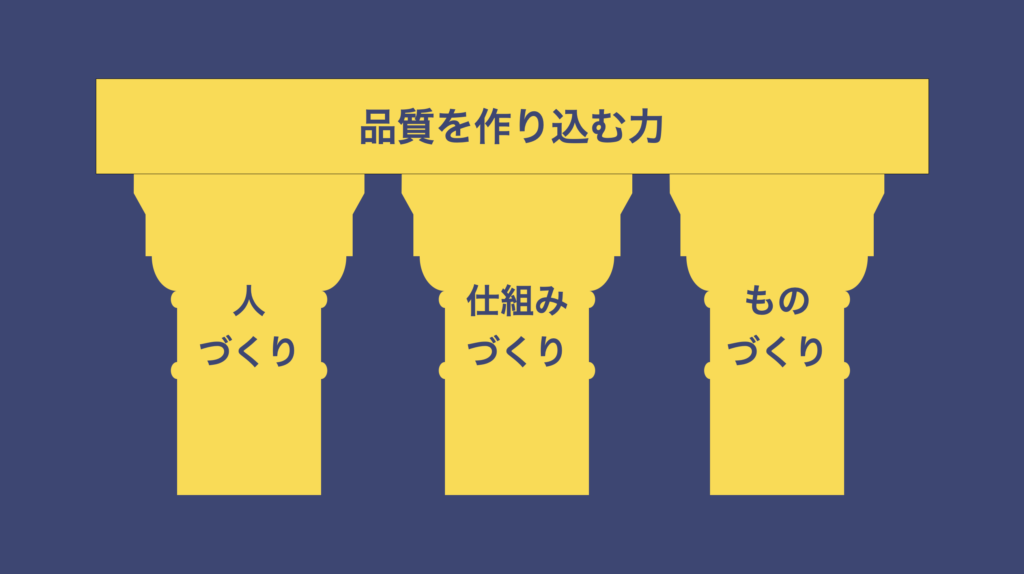
筆者の意見を深掘りしていくと、私としてはこの3つの力は以下のような言い換えができるかと考えています。
人づくり
「品質」が「顧客満足度を満たすこと」であることを認知し、品質を改善する重要性を理解する人を育成していくこと。また、品質を改善するために必要なスキルを習得する機会を体系的に設けること。
仕組みづくり
デザインレビュー(DR)を中心にして開発品の品質を見える化し、全員参加で議論すること。また、品質不良が起きた時に早期解決→再発防止を行うことが仕組みとして定着していること。
もの作り
品質トラブルを未然防止できるように品質リスクを事前に洗い出し、統計的に要求品質が担保されるように製品・サービスの規格値が適切に設定されていること。更に、万が一不良品が製造された際にも検出できる検査能力を備えていること。
これら3つを完全に備えている!と言える組織は少なそうですよね。
技術者の皆さんは、これら3つが適切に運用されているか確認し、改善活動を行うことができれば理想的だと思います。
③未然防止とフロントローディング
未然防止の基本的な考え方
品質トラブルが実際に起きた時は早期対処と再発防止対応が重要となりますが、それ以上に重要となるのは未然防止です。
この考え方は「ハインリッヒの法則」と共通しています。具体的には、実際にトラブルが起きたのは氷山の一角であり、品質トラブルとして表面化し得る要素が水面下には存在しているかもしれません。
ハインリッヒの法則とは、アメリカの労働安全専門家ハーバート・ウィリアム・ハインリッヒが1931年に提唱した安全管理の法則です。この法則は、1つの重大事故の背後には29の軽微な事故があり、さらにその背後には300のヒヤリハット(事故には至らないが危険な状況)が存在するというものです。これにより、事故の発生を防ぐためには、軽微な事故やヒヤリハットの段階で対策を講じることが重要であるとされています。
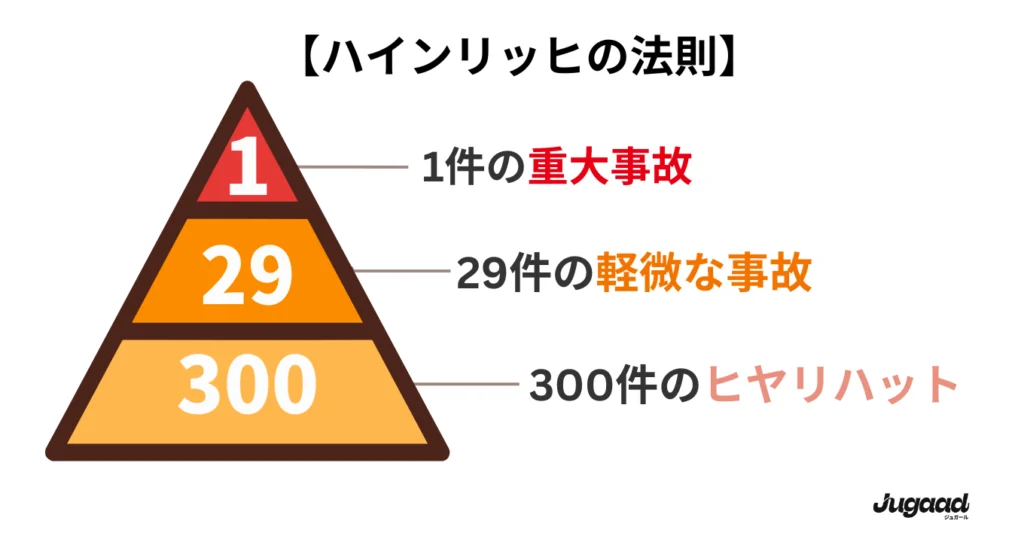
上の図で言うと表面化したトラブルはハインリッヒの法則でいう「重大事故」です。
未然防止は最下層の「ヒヤリハット」に気づくということと同義です。
表面化していないからこそ発見が見逃してしまいがちですが、この表面化していない品質トラブルに気づくことができれば、将来的な損失を回避することができます。
フロントローディング
この未然防止を効率的に実施するためには、「フロントローティング」が有効になるでしょう。
フロントローディングとは、Front(前)にLoading(積載)するという言葉どおり、前倒し可能な作業を製造プロセスの初期段階に詰め込む開発手法である。不具合の予測や製造の効率化を行う「デザインレビュー」、複数のプロセスを各部門が同時並行で進める「コンカレントエンジニアリング」などが代表例だ。
フロントローディングを導入すれば、各プロセス間での手戻りが減り、大幅に工数を削減できる。複数のステークホルダーが存在し、かつ部品単位で分業化されている製造業や建設業などにおいては有用な開発手法といえるだろう。
イメージ図で言うと以下のように開発のピークを開発上流段階にシフトさせることで、開発の手直しを防止する戦略といえます。
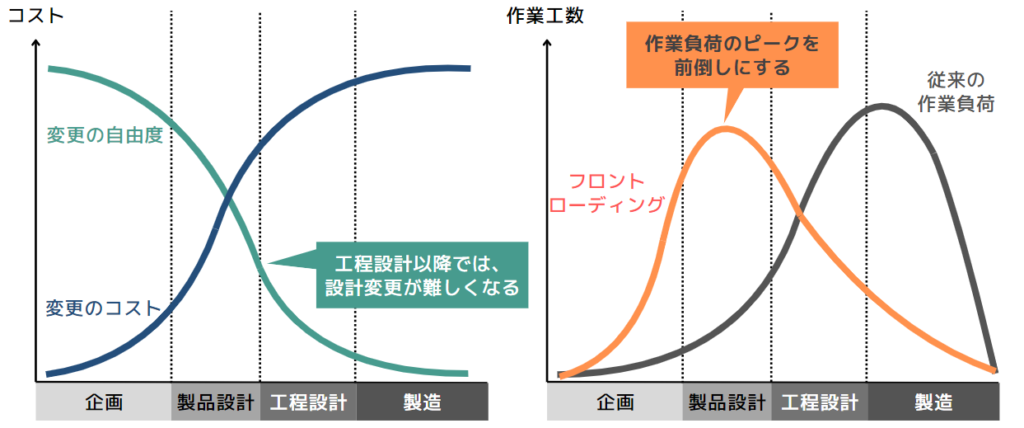
品質不具合が起きてからの対処を通常業務と並行しながら行うことは困難です。また、既存顧客からの信頼を失ってしまえば、会社そのものが無くなってしまうかもしれなせん。
是非フロントローディングの実践、具体的にはデザインレビュー(DR)で複数部門を交えながら開発課題がないか、未然防止ができないのかをゼロベースで考えてみましょう。
トラブルの早期対処と再発防止は「守り」、未然防止は「攻め」の活動といえます。是非未然防止を実施するためのフロントローディングでリスク抽出を行っていきましょう。
まとめ
今回の記事のまとめは以下の通りになります。
- 「品質を作り込む」とは「品質不良品を作らない」、「品質不良品を万が一製造しても市場に流さない」という2つの対策を絶えず行うこと。
- 上記2つの対策を行うためには、「人づくり」「仕組みづくり」「もの作り」の3つが柱となる。
- 品質不良を撲滅する上で最も効果的なのは「未然防止」である。未然防止の実施には「フロントローディング」が有効であり、リスクの事前抽出を行うこと。
今回の記事を参考に今後のQC検定1級に合格していただければ、筆者としてこれ以上ない喜びとなります。
是非私の記事を参考にしていただき、試験に合格された時は連絡をいただけると嬉しいです!
それでは最後に、私の大好きなドラえもんの言葉で今日の記事を締めさせていただきたいと思います。
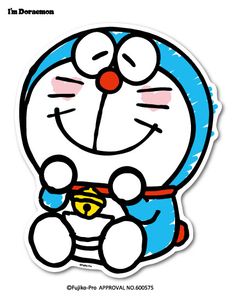
「なやんでるひまに、一つでもやりなよ」
— ドラえもん
今日もありがとうございました!